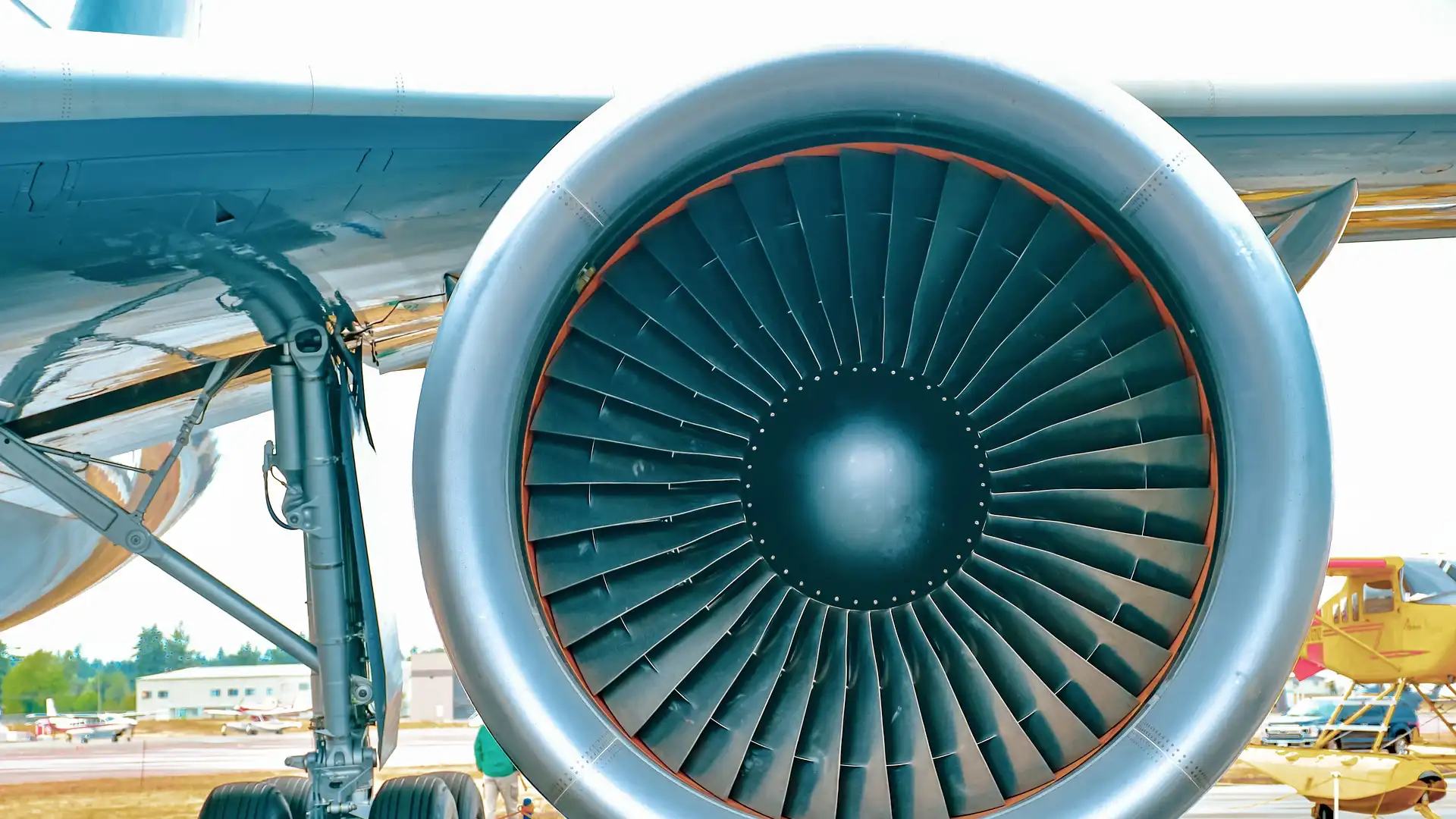
Study on Heat Treatment Process of ASTM A565 XM-32 Stainless Steel

Dr. Robert Anderson
Senior Materials Scientist
Abstract
This study investigates the effect of heat treatment processes on the mechanical properties of ASTM A565 XM-32 stainless steel at room temperature. The results show that when the quenching temperature is 1030°C, the tensile strength and impact toughness reach their peak values. However, the tempering holding time should not be excessively prolonged.
Keywords: ASTM A565 XM-32, quenching temperature, tempering time
Introduction
ASTM A565 XM-32 stainless steel is used for manufacturing turbine wheels in gas turbines. Due to the demanding working environment, the steel must exhibit high strength and impact toughness at room temperature (A_k ≥ 100 J, as per ASTM A565 standards). Additionally, it must withstand a specified temperature (595°C) and load (240 MPa) for 30 hours without fracture in notched composite specimens. To ensure the success of the heat treatment process and avoid repeated treatments, a series of experiments were conducted to determine the optimal parameters.
Technical Requirements
1. Chemical Composition
The chemical composition requirements (mass fraction, %) are listed in Table 1.
Table 1: Chemical composition requirements
C | Mn | Si | Ni | Cr | Mo | V | P | S | N |
---|---|---|---|---|---|---|---|---|---|
0.08–0.15 | ≤0.90 | ≤0.30 | 2.50–3.00 | 11.50–12.25 | 1.50–2.00 | 0.25–0.40 | ≤0.015 | ≤0.010 | ≤0.06 |
Residual elements: Al ≤ 0.05%, As ≤ 0.15%, Sn ≤ 0.10%, Sb ≤ 0.003%.
2. Mechanical Properties at Room Temperature
The mechanical property requirements are listed in Table 2.
Table 2: Mechanical property requirements
R_m (MPa) | R_p (MPa) | A (%) | Z (%) | A_k (J) | HB |
---|---|---|---|---|---|
≥830 | ≥1035 | ≥13 | ≥30 | ≥100 | 321–352 |
Experimental Procedure
1. Material Preparation
The steel was produced using the EAF + LHF + VCD + ESR process. The melting analysis is shown in Table 3.
Table 3: Melting analysis (mass fraction, %)
C | Mn | Si | Ni | Cr | Mo | V | P | S | N | Cr_eq |
---|---|---|---|---|---|---|---|---|---|---|
0.12 | 0.76 | 0.18 | 2.76 | 11.81 | 1.7 | 0.31 | 0.012 | 0.001 | 0.03 | 4.8 |
2. Forging and Processing
- Forging temperature: 880°C–1180°C.
- Samples were forged into Φ60 mm billets and then machined into Φ30 mm specimens.
3. Heat Treatment Schemes
Five heat treatment schemes were tested:
- Quenching at 990°C (1 h, oil cooling), tempering at 560°C (3 h, oil cooling).
- Quenching at 1010°C (1 h, oil cooling), tempering at 560°C (3 h, oil cooling).
- Quenching at 1030°C (1 h, oil cooling), tempering at 560°C (3 h, oil cooling).
- Quenching at 1040°C (1 h, oil cooling), tempering at 560°C (3 h, oil cooling).
- Quenching at 1050°C (1 h, oil cooling), tempering at 560°C (3 h, oil cooling).
Results and Discussion
-
Effect of Quenching Temperature:
- At 1030°C, tensile strength and impact toughness peaked.
- Higher temperatures (>1030°C) led to grain coarsening, reducing strength and toughness.
-
Effect of Tempering Time:
- Extending tempering time to 5 hours caused carbides to coarsen, reducing strength and toughness.
Conclusion
- The optimal quenching temperature for ASTM A565 XM-32 is 1030°C.
- Tempering time should not exceed 3 hours to avoid performance degradation.
- The recommended heat treatment process is:
- Quenching: 1030°C for 1 hour, oil cooling.
- Tempering: 580°C for 3 hours, oil cooling.
References
- Tanaka, T. Ferritic Stainless Steels. Translated by Zhang Jiayuan, Zhang Shaolin. Beijing: Metallurgical Industry Press, 2003.
- China Materials Engineering Canon (Vol. 3): Iron and Steel Materials Engineering (Part 2). Beijing: Chemical Industry Press, 2005.
- Cui Zhiwu, Cao Zhenchun. Metallurgy and Heat Treatment, 2nd Edition. Beijing: Mechanical Industry Press, 2007.
SEO Optimization Notes:
- Title: Includes key terms like "ASTM A565 XM-32" and "heat treatment" for searchability.
- Keywords: Highlighted for SEO.
- Structured Content: Clear sections (Abstract, Introduction, Results, Conclusion) improve readability and indexing.
- Technical Details: Tables and specific parameters enhance relevance for technical searches.
- Citations: References add credibility and depth.